Published: August 2nd 2016
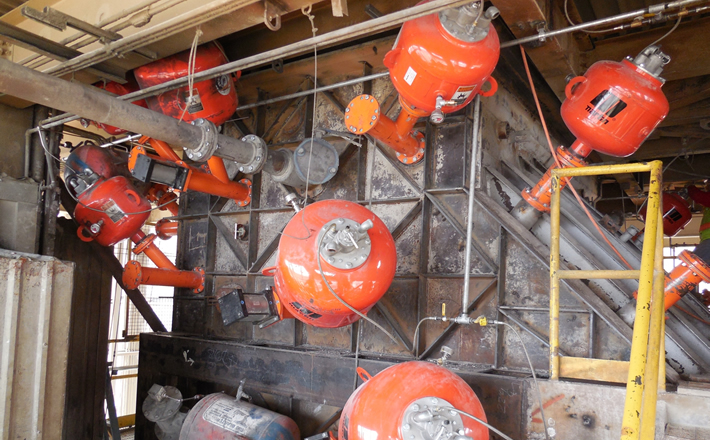
Efficient material flow is a vital element to profitability. Hang-ups in storage systems and buildups in process vessels can choke material movement, causing bottlenecks that create expensive complications to equipment performance and productivity. Poor material flow also increases maintenance expenses, deterring manpower from fundamental tasks.
If they become severe enough, flow problems can bring production to a complete halt. When blockages become that significant, they often require high-pressure water washing, CO2 blasting or other manual cleaning, which can accelerate wear on refractory surfaces or even directly cause damage.
Battling Build-Up
Air cannons have proven to be an effective flow aid device for over 40+ years of use in cement manufacturing, ash handling, rock crushing and other applications. Also known as air blasters, the technology helps improve throughput and reduce material build-up with a powerful discharge of air, dislodging accumulation that impacts process efficiency. In the cement industry, air cannons are frequently specified to eliminate build-ups in preheater towers, precalciners, riser ducts, feed shelves, cyclones and tertiary ductwork. They have also seen extensive service on clinker coolers, in material transfer chutes and in storage bunkers.
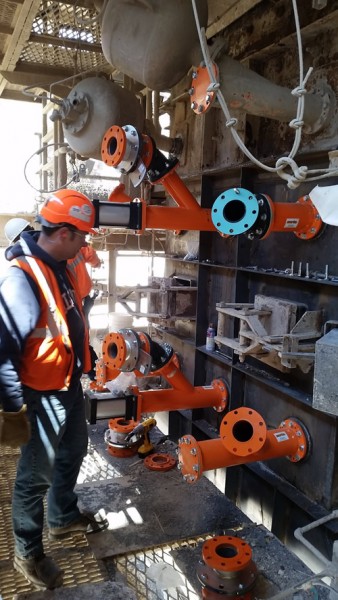
Introduced in the early 1970s, air cannon design has been improved throughout the years, leading to enhanced cleaning performance, energy efficiency and safety. Among the upgrades is a high-speed valve design that can be mounted on a smaller air reservoir, delivering higher discharge forces than less efficient valves on larger tanks. The new generation of valves produces about twice the blast force output of the designs introduced just a decade ago, allowing users to save energy by using much less compressed air volume.
Another energy-saving development is the piston return reservoir. During the air cannon’s firing sequence, the pressure in the return reservoir approaches that of the tank, but the fast-acting valve closes when about 50% of the tank’s original pressure remains. The peak force output remains the same, but air consumption is dramatically reduced, easing the demand on plant air supply and reducing cost.
With the introduction of new positive-firing valves, air cannons have also become safer in recent years. The cannons respond to an air pressure surge delivered by a solenoid valve; in order for the cannon to fire, a positive signal must be received. Unlike negative pressure-firing designs, a cannon equipped with this new type of valve will not discharge accidentally in response to a drop in pressure, so an interruption in air supply or a broken line cannot trigger it.
With valve cycles measured in milliseconds and efficiency at an all-time high, some engineers believe that contemporary innovations have pushed air cannon performance to its limits. As a result, more R&D effort is now being directed at the nozzles themselves, which create the air pathway that actually contacts the accumulated material. Product designers are finding evidence to support the belief that new nozzle designs still hold significant potential for improving overall effectiveness, particularly in applications with difficult materials or harsh operating conditions.
New Nozzle Designs
A critical component is the heat-resistant nozzle, designed and manufactured to deliver the optimum force and blast pattern to suit the application. These nozzles are currently available in a variety of shapes, sizes and materials of construction. In recent years, the most commonly used are cast alloy fan shapes and stainless steel pipes. While a pipe nozzle is reasonably light and easy to install, it has a limited area of influence on a flat vertical wall. In contrast, the fan nozzle typically has a wide area of influence and shorter range, but frequently weighs in at 70 pounds or more, making it hard to install and even more difficult to replace. Installing fan nozzles is especially problematic on an existing system, as it requires torch cutting the vessel wall, removing the refractory, then holding the heavy component in the correct position while it’s welded in place.
With more focus on nozzles as a way to improve system performance, better customization of blast patterns and forces to suit the materials and process conditions of individual operations can be achieved. The nozzle is the component that takes the stored energy in the form of compressed air and directs it to do work, so it has a dramatic effect on the performance of any air cannon. The application dictates the type of performance needed, including the shape of the air blast, length of the plume, etc. In addition to dislodging accumulated material, a goal in every application is to use the stored energy as efficiently as possible.
Further advancement in nozzle technology over the last few years include a 360º retractable design that extends into the material stream only during the firing cycle to protect itself from extreme temperatures and abrasion. This innovative design solves two common industry problems: effectively dislodging accumulations in hard-to-reach areas without shutdown or manual labor, while significantly extending nozzle life. Further, the retractable nozzle can be serviced from outside the vessel, reducing service time and risk of injury.
![]() Recessed |
![]() Extended |
Retractable nozzles extend only during the firing cycle, protecting against damage from extreme temperatures and abrasion. |
Many air nozzles used in today’s high-performance cannons are similar to the designs used 20 years ago. Manufacturers offer a range of shapes, sizes and blast patterns to accommodate different materials and process conditions, but nozzle styles and performance have not changed significantly. Even after its long service history as a material flow technology, air cannon users still have a relatively small inventory of nozzle choices for high-temperature applications.
CFD Modeling
Among the obstacles to new nozzle development has been the lack of precision in existing mathematical models for predicting the performance of new designs, particularly with respect to specific materials or conditions. While existing Computational Fluid Dynamics models could simulate nozzle performance in theoretical terms, the results often varied from the actual performance observed in a customer’s process. In addition, prototype manufacturing has traditionally been time-consuming and expensive, further slowing the R&D process. Selecting the optimum nozzle for specific customer operating conditions often took multiple iterations, making subtle changes to obtain the most effective configuration for that operating environment.
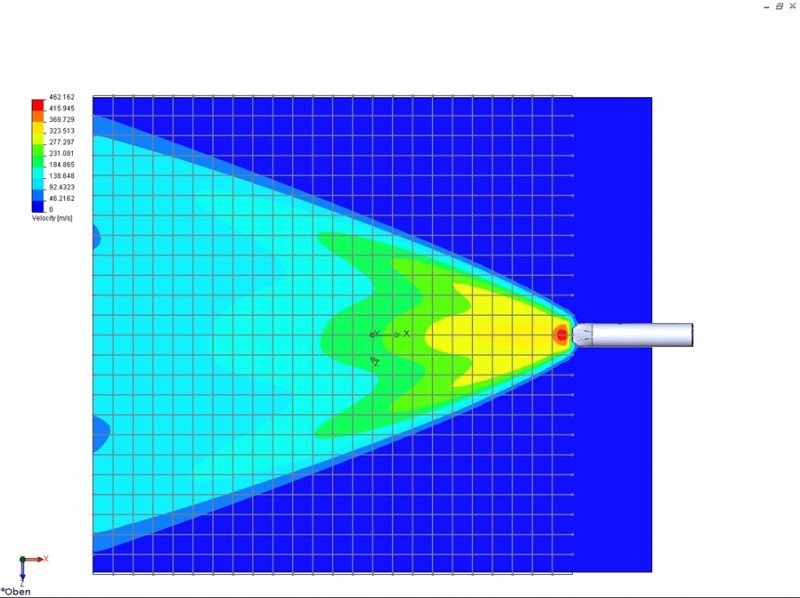
With the recent advances in numerical flow simulation software and the advent of rapid prototyping techniques, Martin Engineering researchers felt it was time to create a more accurate standardized model and focus on designing new and innovativenozzles to further enhance air cannon performance. The objectives included development of a predictive theory that better reflects actual performance, accelerating the process from concept to prototype and drastically reducing trial-and-error tactics.
If successful, the result would be more effective cleaning performance from air cannon systems, with nozzle designs tailored to individual operating conditions. It was expected that engineers would also develop a deeper understanding of customer processes and promote product development that would be truly process-oriented. The benefits would include current product optimization, cost savings and faster development times, ultimately giving customers a wide selection of nozzles.
The investigation began with off-the-shelf software and CFD theory. Researchers plugged in the physical parameters of existing Martin Engineering nozzle designs and computed a projected blast pattern for each one. The nozzles were then taken to a test station known as a blast table, where they were mounted on a cannon and aimed at a horizontal surface covered with sand. By firing the cannon across the sand, investigators could obtain an accurate representation of the actual pattern for each nozzle design, which was then compared to the area of influence predicted by the software.
Following this series of tests, Martin researchers then revisited the CFD modeling program and made progressive adjustments, eventually resulting in a model that accurately reflected the blast patterns of the company’s existing nozzle shapes and sizes. Investigators then turned to the development of new nozzle designs which could be tailored for specific customer operations and process conditions.
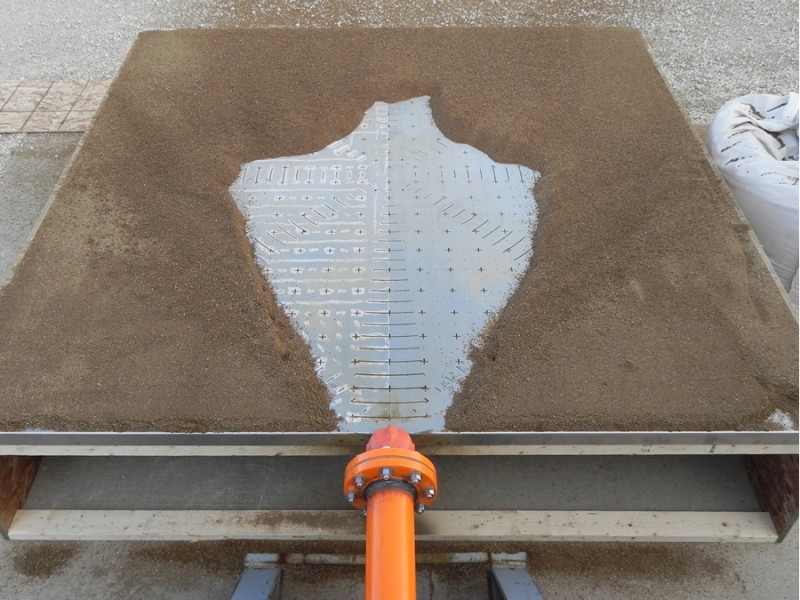
By progressing beyond a standard range of nozzle configurations from which the best-available solution would be chosen for a given application, the objective was to develop the ability to efficiently design and test nozzles developed specifically to suit individual customer processes, thereby delivering more effective cleaning under virtually any circumstances. Further, the customized CFD model would allow the R&D staff to accurately predict the forces and blast patterns resulting from any new nozzle design, without resorting to the expensive and time-consuming process of prototyping and physically testing every one.
First Development
The first nozzle development project using the new CFD modeling technique was initiated to address one of the most common problems shared by high-temperature air cannon users. Replacement of conventional fan-type air cannon nozzles is a difficult and laborious process that affects virtually all systems at some point. The least disruptive time to install is during construction of a new system or assembly of a new vessel. When the air cannon system is designed-in from the beginning, technicians can cut the necessary access holes and weld the nozzles in place with relative ease. Refractory can then be fitted around the nozzle opening. But when nozzles fail and require replacement, the process is much more complicated.
Replacing a conventional fan nozzle on existing equipment requires the removal of refractory material from around the nozzle opening, typically with a pneumatic hammer. The process invariably weakens the surrounding refractory and renders it more susceptible to spider-webbing and subsequent cracking. The air cannon is disassembled from the air supply pipe from outside the vessel and the failed nozzle is cut from the vessel or pipe, usually with a torch. The new nozzle is welded into place and the damaged refractory is patched, followed by the re-installation of the cannon outside the vessel. In addition to the potential refractory damage, the process is labor-intensive, requiring an extended system shutdown and also introduces the risk of injury from working in a confined space. A key issue is the risk of misplacement, which drastically affects a cannon’s effectiveness.
Because of the time required to install fan jet nozzles and the potential for refractory damage, many companies elect to install a conventional pipe nozzle. Unfortunately, pipe nozzles have a smaller area of influence and are generally unable to deliver the same cleaning action as a fan jet nozzle. So Martin Engineering researchers went to work on designing a type of hybrid, one that would deliver cleaning performance equal to standard fan jets, yet be as easy to remove and replace as a pipe nozzle.
Using the modified CFD model, the R&D staff conducted virtual testing on several different nozzle configurations, continually refining the size, shape and orifice to investigate the changes in blast pattern. By eliminating the need to prototype and physically observe each design, researchers were able to quickly narrow down the most likely candidates to a very small list.
The patent-pending quick-change nozzle design that evolved from that investigation proved that the R&D team could achieve fan jet performance and combine it with the quick access which in the past had only been available from a pipe nozzle. The CFD model had been demonstrated in a real-world situation, helping the R&D team solve a problem that has confronted air cannon users for years.
The benefits are expected to include reduced damage to refractory brick and shorter nozzle service times. By avoiding the need for confined space entry, the new design has eliminated much of the potential risk involved with the change out process. It also allows system operators to add air cannons to an existing process during a brief shutdown, without completely cooling down the entire system to allow entry into the vessel.
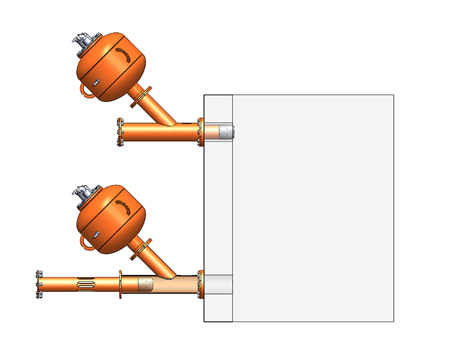
In addition to helping researchers solve a specific problem, the process of developing the quick-change nozzle design and field-proving its effectiveness confirmed the utility and accuracy of the customized CFD model. The Martin R&D team now has confidence that they could approach any process experiencing particle accumulation issues and quickly design and manufacture a nozzle to deliver the optimum blast pattern for that specific application. No longer will air cannon users be limited to off-the-shelf choices or lengthy development times to test new designs.
Conclusions
The benefits of specifying high-efficiency air cannon systems include lower energy costs, reduced maintenance, improved safety, and greater total output.
By customizing existing computational modeling software, Martin Engineering researchers have developed and confirmed an accurate method of predicting nozzle performance under specific operating conditions, allowing the company to develop nozzle designs for optimum effectiveness, while significantly reducing time-to-market. In fact, Martin Engineering researchers have already used the model to project the performance of hundreds of new nozzle designs.