Tracker™
The Martin® Tracker™ provides immediate, continuous precision adjustment of wandering conveyor belts. The Tracker™ works where other belt training devices fail to reduce edge damage, prevent spillage and extend belt life.
Features and Benefits:
- Keeps the belt in alignment with automatic, continuous adjustments
- Improved tracking reduces edge damage, spillage and maintenance expense
- Continuous precision adjustment of the patented parallel steering/training system keeps the belt tracking properly
Options:
The Martin® Tracker™ is available in 3 models to match the requirements of each application.
- The Tracker™ is designed for applications under typical industrial material handling conditions.
- The Tracker™ HD is designed to withstand the stress associated with wider, thicker belts moving at higher speeds and carrying heavier loads.
- The Tracker™ XHD is engineered to be effective in the most rugged of applications.
Our technicians and engineers are available to provide expert advice and assistance on this product and all of your bulk material handling questions and problems. Please contact us today and let us help!
Belt Alignment Products Prevent Excessive Wear And Extend Belt Life
Transfer Point Solutions Result In Safer, More Productive Coal Mining
Power Plant Needs Cleaner, Safer, More Productive Material Handling System
MartinPLUS® Installation Services Redesign Power Plant Transfer Points
Martin® Tracker™ Corrects Conveyor Belt Misalignment At Steel Complex
Martin Designs Special Suspension Bracket On Suspended Conveyors
Transfer Point Solutions Increase Productivity At Container Board Plant
Martin® Tracker™ Corrects Conveyor Belt Mistracking
Deteriorating Power Plant Needed Material Handling System Redesign
Cement Plant Gets Extensive Conveyor System Overhaul
Tracker™ Installation Corrects Spillage and Fugitive Material
Transfer Point Solutions Correct Conveyor Belt Mistracking
Sand Plant Experiences Spillage And Carryback Before Martin Steps In
Conveyor Belt Inspection Identifies Carryback And Belt Wandering
Belt Misalignment Causing Structural and Belt Damage
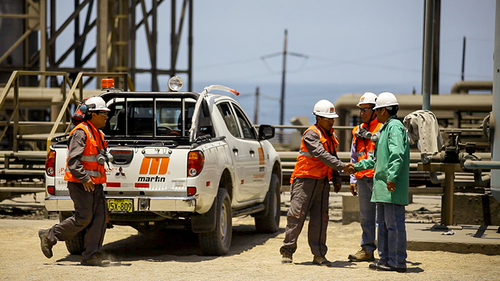
Free Engineering and Application Assistance
Our technicians have solved problems for people in your industry all over the world. Take advantage of our wealth of knowledge. Tell us about your situation today to learn how Martin can improve your performance, safety and bottom line - with no obligation. We want to ensure that you choose the right solution for your exact needs and we are willing to invest the time upfront to get it right the first time.
Briefly Describe Your Application